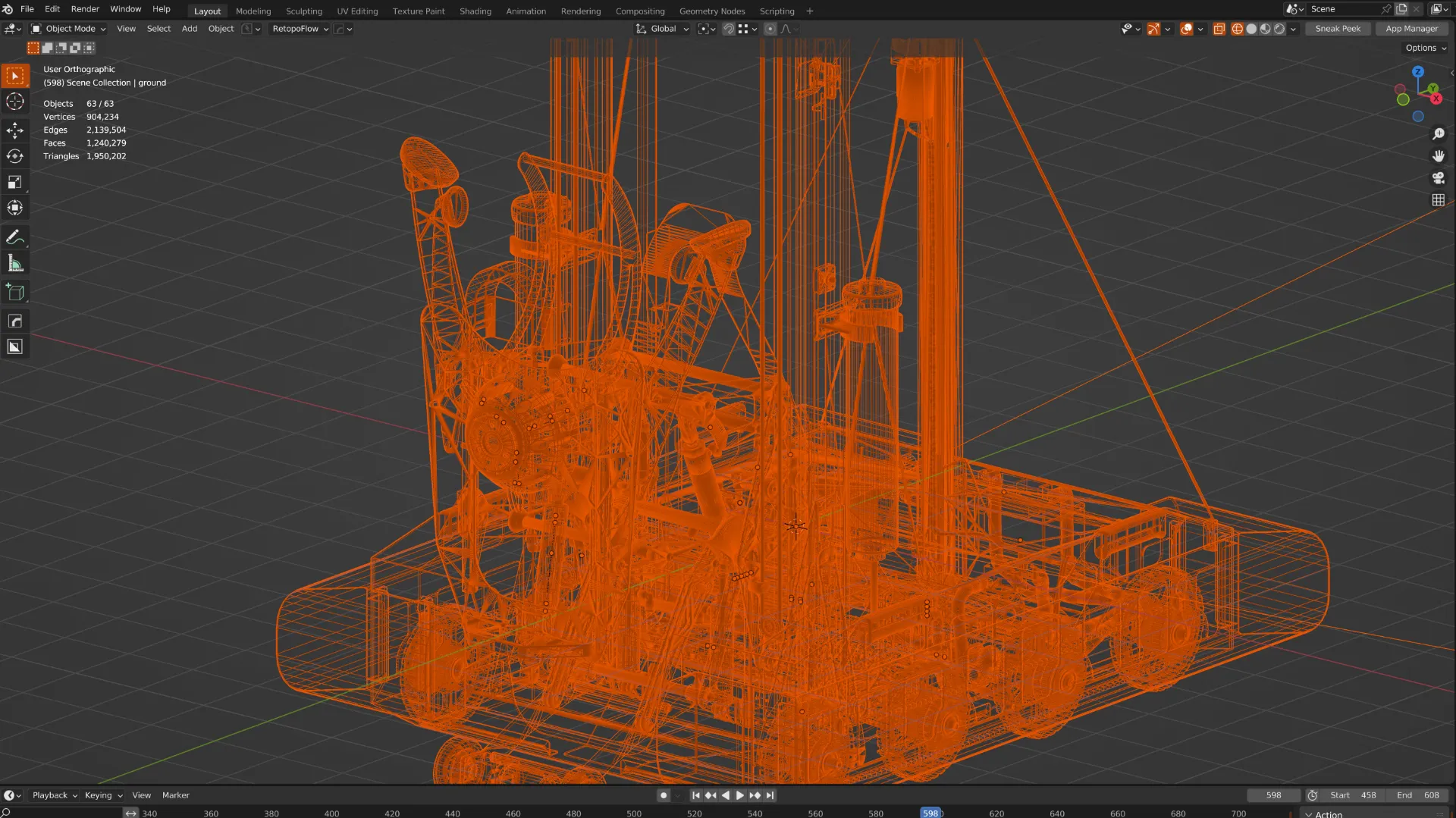
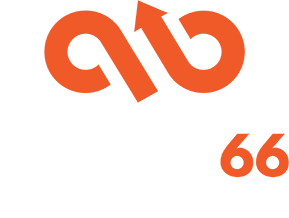
Robotique FIRST Québec contacted Route 66 Digital in 2022 with an idea of creating an online interactive learning experience for students that could be explored at their home or in the classroom. They had created a CAD model of an existing competition robot and had created their first interactive but they were not achieving their performance goals and not making significant progress towards their delivery dates. Shortly after they reached out to Route 66 Digital a partnership was formed to bring the concept to life using Blender and Verge3d.
The first phase, code named the January Build, was developed to achieve two goals. The first was to optimize the current CAD model. The second goal was to design and develop a kiosk interactive that would be a proof of concept for the FIRST Tech Challenge in January 2023. The Robot Explorer – January Build reached an early milestone and is now working as web based interactive. Although not fully optimized, the goal of having the application work online was achieved and can be experienced here.
The second phase, code named the March Build, will be an updated version of the January Build and will contain additional animated elements for exploration. The March Build will have additional model optimization and will be exhibited at the FIRST Robotics Competition on March 31st, 2023.
The third and final phase is currently code named the Summer Build. This build will be a fully optimized model with an entirely new user interface to handle the numerous interactive parts, components and lesson plans that are still in the process of being developed.
For the January Build the focus has been primarily on model optimization. The original CAD model had over 2200 parts and was over 30 million triangles with a file size over 2 gigabytes. The goal of each mesh is to reduce the CAD model triangle count to 1.6% of its original count. In doing this, three levels of model detail have been created, High (optimized topology with no triangle limit), Medium (derived from a High mesh with a triangle reduction of 10:1) and Low (derived from a Medium mesh with a triangle reduction of 60:1 or lower). The January and March builds uses a mix of Low, Medium, High and CAD models. The final summer build with a target of 500,000 triangles will primarily be Low and Mid to reach our target triangle count.
Unlike traditional models where components that are not seen can be ignored, the ultimate interactivity for the Summer Build requires that every component be optimized so that students can explore deep within the components to see how parts interconnect.
For the January build 15% of the CAD meshes were optimized based on the highest triangle count and those with multiple duplicates. This process allowed us to quickly decrease the triangle count from 30 million to 3 million.
Flat vs Smoothed shading - CAD models when imported into Blender arrive with nearly every edge marked as sharp and no smoothing groups, leading to very flat rendered surfaces. The optimized models, created in Blender, have sharps on required edges and auto smoothing producing nice smooth curved surfaces within the limits of the target triangle count for each object as described above. The January Build had many objectives: a proof of concept, a work in progress milestone and a kiosk to be shown to partners and investors but most importantly, the output could not impact the continuing development of the March and Summer builds. With these factors in mind, the January Build left many components not shaded smooth that will be updated in subsequent builds.
Thank you for contacting Route 66 Digital! We will reply to you shortly.